Case Study 1
Enhanced Safety and Efficiency with Automated Chemical Handling and Processing (Production)
Challenges
Traditional chemical production often relies on manual handling of hazardous materials, leading to safety concerns and potential human error. Chemical companies struggle to ensure worker safety, maintain consistent product quality, and optimize production efficiency.
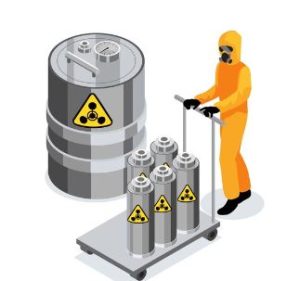
Solution
Chemical companies can implement automated chemical handling and processing systems. These systems utilize robots and enclosed conveyor belts to transport and manipulate hazardous chemicals throughout the production process. Automated dispensing systems can precisely measure and mix different chemicals according to pre-programmed recipes. Additionally, integrated sensors can monitor reaction temperatures, pressures, and other parameters for real-time process control.
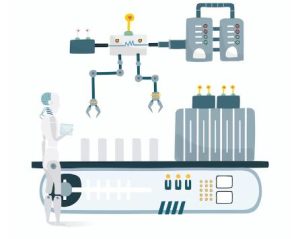
Benefits
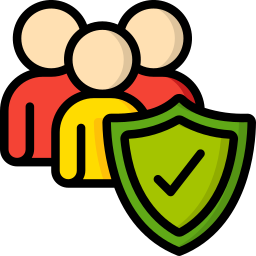
Enhanced worker safety by minimizing human interaction with hazardous chemicals.
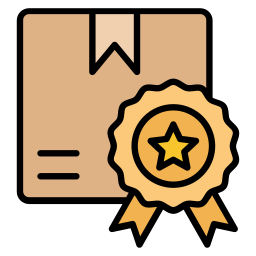
Improved product quality and consistency with precise automated handling and controlled reaction environments.
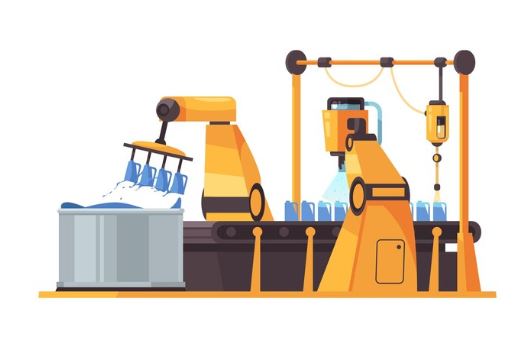
Increased production efficiency due to faster processing times and reduced reliance on manual labor.

Reduced risk of human error and potential accidents during chemical handling and processing.
Case Study 2
Real-Time Process Monitoring and Predictive Maintenance with Connected Equipment (Operations)
Challenge
Traditional chemical production relies on periodic maintenance schedules and limited data insights. Chemical companies struggle to identify potential equipment issues before they cause breakdowns, leading to production disruptions and potential safety hazards.
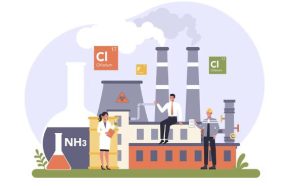
Solution
Chemical companies can implement a connected factory approach. Production equipment can be equipped with sensors that monitor vibration, temperature, pressure, and other critical operating parameters. This data is transmitted securely to a central platform for real-time analysis. Predictive maintenance algorithms can identify potential equipment failures based on sensor data and historical trends, allowing for proactive maintenance interventions.
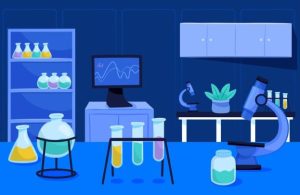
Benefits
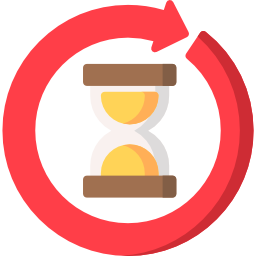
Reduced downtime and production disruptions through proactive maintenance based on predicted equipment issues.
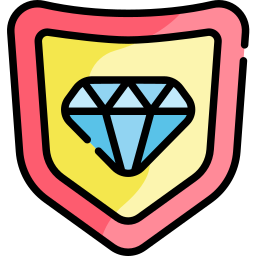
Enhanced equipment performance and extended lifespan through preventive maintenance practices.
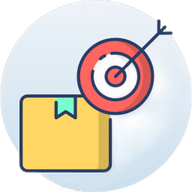
Optimized resource allocation in the hospital, leading to cost saving• Improved safety by identifying potential equipment malfunctions before they lead to accidents.s and improved operational efficiency.
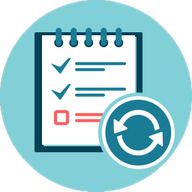
Data-driven decision making for prioritizing maintenance needs and optimizing resource allocation.
Case Study 3
Smart Warehousing with Automated Storage and Retrieval Systems for Efficient Inventory Management (Logistics)
Challenge
Traditional chemical warehouses rely on manual forklift operations and static storage configurations, leading to inefficiencies in space utilization and time spent on material handling of potentially hazardous materials. Chemical companies struggle to ensure safe storage practices, optimize warehouse operations, and improve order fulfillment speed.
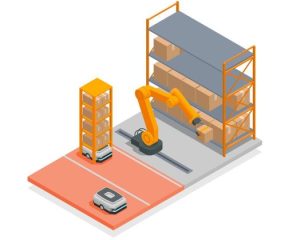
Solution
Chemical companies can implement automated storage and retrieval systems (AS/RS) designed for hazardous materials. These systems utilize robots or automated shuttles operating within designated containment zones to store and retrieve chemicals on high-density shelving units. Warehouse management systems (WMS) can be integrated with chemical safety protocols for proper storage and handling procedures.
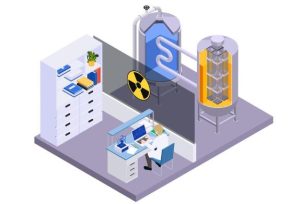
Benefits
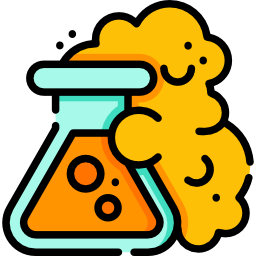
Increased safety by minimizing manual handling of hazardous chemicals within the warehouse.
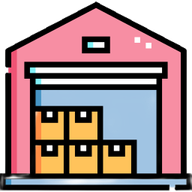
Improved space utilization and storage capacity through high-density shelving configurations.
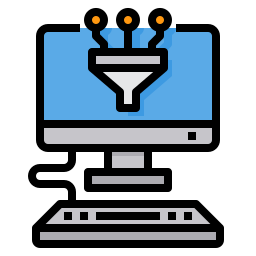
Enhanced operational efficiency and faster order fulfillment times with automated retrieval systems.
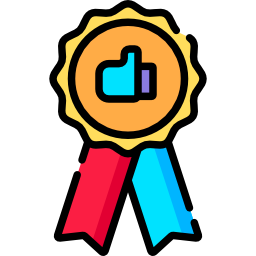
Streamlined inventory management and real-time tracking of chemical inputs and finished products.
These cases showcase how automation technology can benefit chemical companies across production, operations, and logistics. By implementing automated systems, real-time process monitoring, and smart warehousing solutions, chemical companies can improve worker safety, optimize production processes, minimize disruptions, and ensure efficient inventory management for hazardous materials.