Optimizing Performance: Rootfacts Company's Computer-Aided Engineering (CAE) Software for the Plastics Industry
For the plastic industry, it is all about innovation and pushing the limits of material science and design. Plastic has a crucial role in many applications ranging from lightweight yet robust automotive components to very intricate medical devices. However, this calls for a sophisticated approach in terms of maintaining performance, safety and functionality of these plastic products. This is where Computer-Aided Engineering (CAE) software comes in – an arsenal of powerful tools that allow engineers to analyze, optimize and validate designs of plastic parts before any physical prototypes are produced.
Rootfacts Company is a leading provider of services to the plastics industry well aware of this transformative potential offered by CAE software. We offer an extensive range of CAE solutions tailored specifically to meet the unique requirements of manufacturers operating within the plastics sector. This detailed guide examines how Rootfacts CAE software enables businesses to manufacture better plastic products, reduce costs associated with development as well as speed up time-to-market.
Unlocking the Power of Computer-Aided Engineering for Plastic Engineering
Traditional approaches towards developing plastics involved physical prototyping and testing which were quite resource-intensive as well as time-consuming. On top of introducing a virtual testing environment where designs can be tested under various conditions, CAE software revolutionizes this practice. Here’s how CAE software empowers plastic engineers:
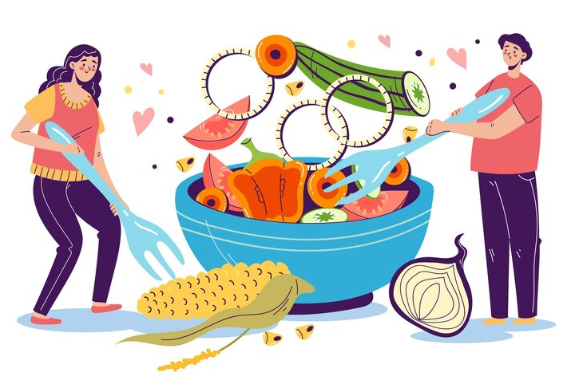
Improved Design Validation
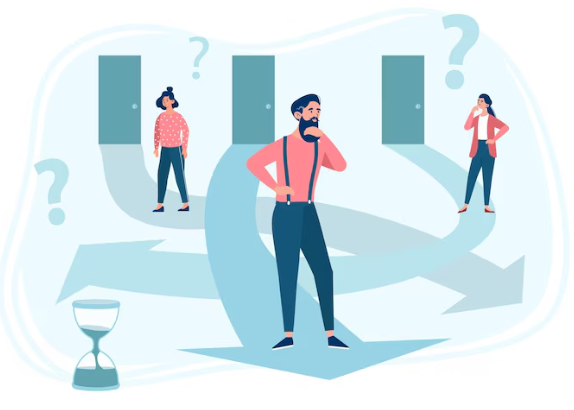
Material Characterization
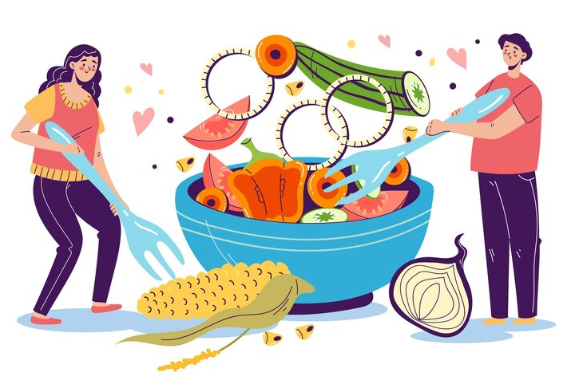
Design Optimization
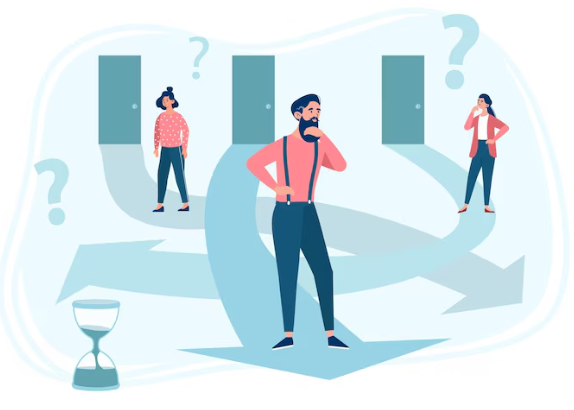
Mold Design Analysis
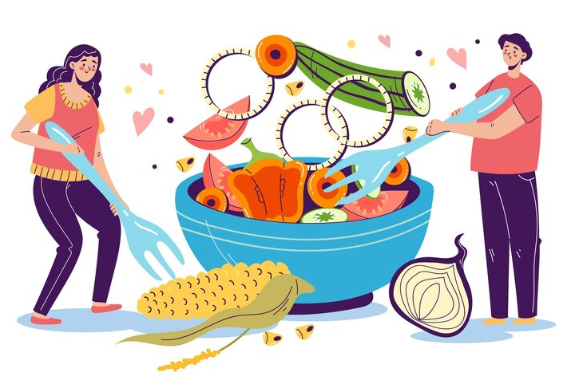
Predictive Maintenance
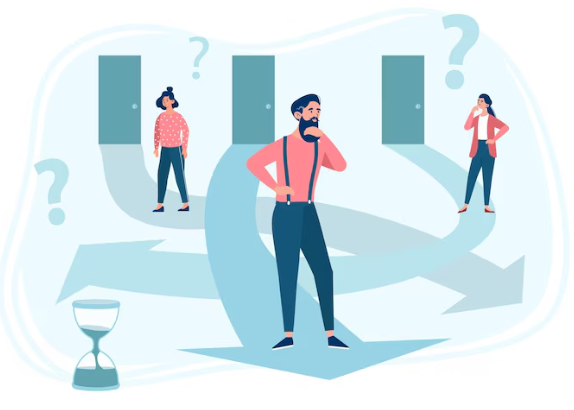
Cost Reduction
Rootfacts Specialized CAE Solutions for Plastics
While there are many advantages that come with using generic CAE software, Rootfacts Company takes an extra step. Our CAE solutions specifically target the complexities of plastic engineering thus uniquely satisfying requirements within the plastics industry:
Injection Molding Simulation
Specifically designed tools by Rootfacts CAE software allow simulating injection molding process which involves studying flow patterns; gate freeze time; warpage and residual stress within molded parts. High-quality plastic parts with minimal defects can be obtained by manipulating these parameters
Mold Filling Analysis
The software created by Rootfacts has tools that enable one to analyze the behaviour of filling up molds including air traps, short shots and weld lines. This approach helps in ensuring effective mold filling, reducing wastage of material as well as doing away with any potential defects in the parts.
Material-Specific Modeling
Our software integrates advanced material models representing different kinds of plastics accounting for non-linearity creep as well as anisotropy factors. As a result simulation results are accurate and predictions made about part performances become dependable.
CAD/CAM/CAE Solutions
Within our computer aided engineering solutions suite, we have integrated with well known FEA tools that offer detailed analysis for stress and strain in plastic materials. In these way, engineers are able to forecast the performance of different materials under various loading conditions and optimize their designs for structural integrity.
Multiphysics Simulation
Our advanced computer aided engineering software provides multiphysics simulations, which allow engineers to analyze combined effects of stress, strain, temperature and fluid flow on plastic parts. As such, this helps us appreciate the overall dynamics of the part’s performance under real life conditions.
The Rootfacts Advantage: Features and Benefits
Rootfacts CAE software for the plastics industry offers a robust suite of features designed to empower your engineering teams:
User-Friendly Interface
We know that intuitive controls can simplify workflow. Thus our software entails an unique interface that makes it easy for individuals who will operate it as though they were already familiar with CAD functions.
Pre- and Post-Processing Tools
These include pre-processing tools for model set up data visualization post-processing tools for result interpretation etc.