Quality Control And Inspection Systems Solution for the Mastering of Plastic Production by Rootfacts
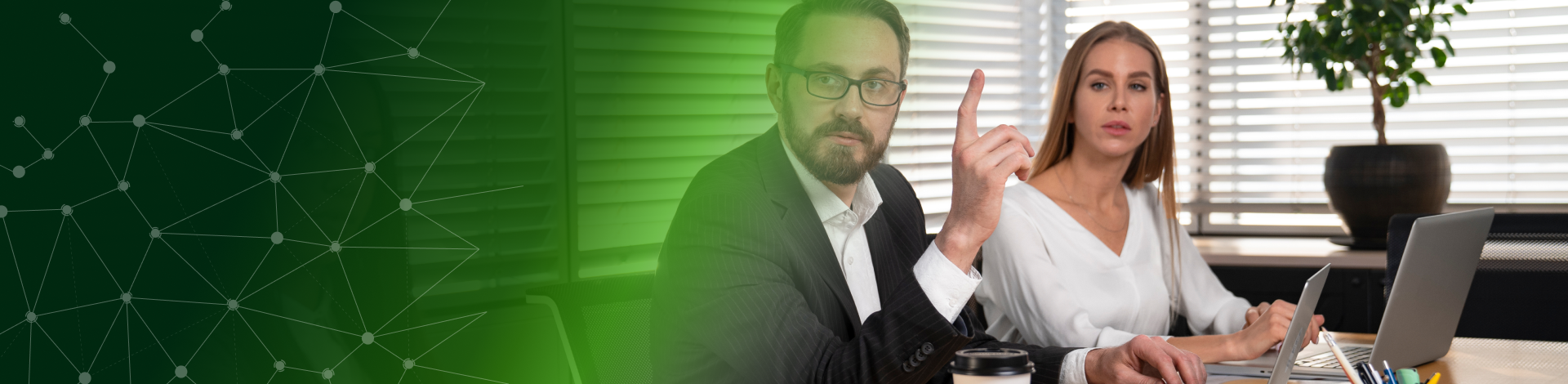
Plastics are in constant pursuit of new ideas and are very precise. It has been observed that plastic products have become an integral part of our lives, from one-time-use packaging to high-performance engineering components. However, it is critical to maintain uniformity within the entire process of manufacturing. This is where Rootfacts comes in with its comprehensive suite of Quality Control (QC) and Inspection Systems exclusively for the plastics industry.
Significance of Quality Control in Plastics Manufacturing
Maintaining quality in production of plastics has several benefits in plastic industry
Product Safety and Performance
Shoddy plastic items may be dangerous or fail to function as expected. QC ensures adherence to regulatory standards and customer specifications.
Brand Reputation
A renowned brand is built on consistent output quality which leads to consumer loyalty. Conversely, defects can destroy a firm’s reputation as well as lead to expensive recalls.
Cost Reduction
By identifying problems early enough during production cycle, there is reduction in waste and rework time resulting into saving money.
Process Optimization
Through QC data it will be able to identify bottlenecks and areas that needs improvement hence facilitating a more streamlined and efficient process of production.
Rootfacts QC and Inspection Systems: A Complete Solution
Rootfacts recognizes the unique challenges facing plastic manufacturing. Our QC and Inspection Systems take these challenges head-on; empowering businesses with enhanced quality control abilities. Here are some solutions we offer:
Visual Inspection Systems
- Machine Vision Systems (MVS)
These systems utilize advanced cameras together with image processing software which allows automation of visual inspections like detecting surface flaws, color inconsistencies or dimensional inaccuracies at great accuracy levels and speed.
- Human-Machine Collaboration (HMC) Systems
This technology integrates MVS with human supervision so that trained personnel can either verify complex defects or make subjective judgments about product quality.
Dimensional Inspection Systems
- Coordinate Measuring Machines (CMMs)
These systems are highly accurate and use touch probes or laser scanners to measure the critical dimensions of plastic parts so as to ensure they conform to their design specifications.
- Non-Contact Measurement Systems
For instance, Rootfacts has non-contact measurement tools like laser scanners and vision systems that can be used in measuring complex geometries or fragile components without causing any damage.
Material Testing Systems
- Material Analyzers
These equipment examine the chemical composition and physical properties of raw materials and finished products in order to ascertain if they meet the required specifications for performance and safety.
- Mechanical Testing Systems
In this case, we provide tensile testers, impact testers, among other apparatuses that are employed in studying mechanical attributes of plastics such as strength, flexibility and impact resistance.
Non-Destructive Testing (NDT) Systems
- Ultrasonic Testing (UT)
UT utilizes sound waves to detect internal defects like cracks, voids, and inclusions within plastic parts without damaging the material.
- X-Ray Inspection
X-ray systems offer interior imaging of plastic parts while also revealing hidden defects that guarantee structural integrity.
The Rootfacts Advantage: Why Choose Us for Your QC Needs
Rootfacts does not just offer QC and inspection systems. We deliver a holistic package which includes;
Customization
Integration
Training and Support
Ongoing Support
Quality Investment: Return on Investment
Implementing Rootfacts quality control and inspection systems is beneficial to your plastic manufacturing company in a number of ways: