Case Study 1
Precision Metal Cutting and Fabrication with Robotic Systems (Production)
Challenges
Traditional metal manufacturing relies on manual cutting and fabrication processes, leading to inconsistencies, potential for human error, and dependence on skilled labor. Metal companies struggle to achieve tight tolerances, maintain high production volume, and minimize material waste during cutting.
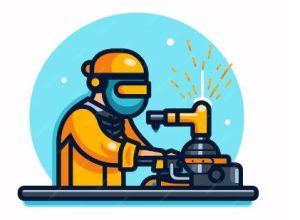
Solution
Metal companies can implement robotic cutting and fabrication systems. Industrial robots equipped with specialized tools like plasma cutters, welding torches, or laser cutting heads can perform precise cutting and shaping of metal components. These systems can be programmed for complex geometries and high repeatability, ensuring consistent results. Additionally, robots can be integrated with automated material handling systems for efficient loading and unloading.
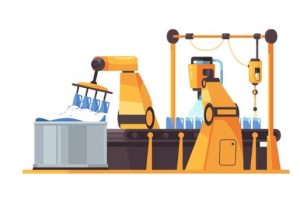
Benefits
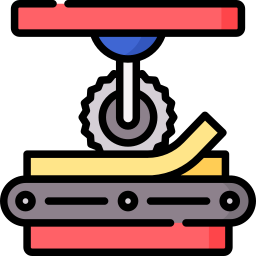
Increased production volume and faster turnaround times with automated cutting and fabrication processes.
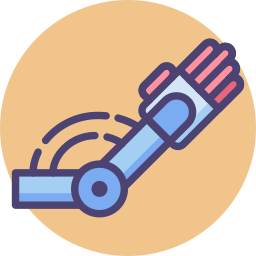
Improved product quality and consistency through precise robotic movements and repeatability
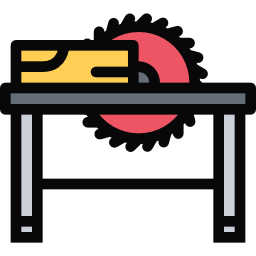
Reduced reliance on skilled labor for manual cutting and fabrication tasks.
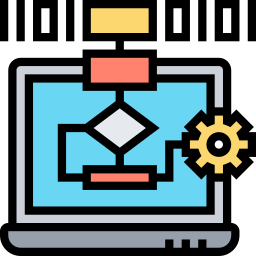
Minimized material waste due to efficient cutting patterns and automated nesting algorithms.
Case Study 2
Real-Time Production Monitoring and Data Analytics for Optimized Resource Management (Operations)
Challenge
Traditional metal manufacturing relies on limited data insights and manual production tracking. Metal companies struggle to identify bottlenecks in production workflows, optimize resource allocation, and make data-driven decisions for process improvement.
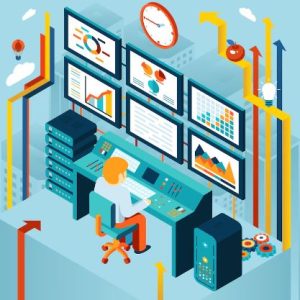
Solution
Metal companies can implement a network of sensors and data collection systems across their production facilities. Machine sensors can monitor performance parameters like power consumption and identify potential maintenance needs. Production line sensors can track material flow and identify bottlenecks. This real-time data is aggregated and analyzed by a central platform to provide insights into overall equipment effectiveness (OEE) and production efficiency.
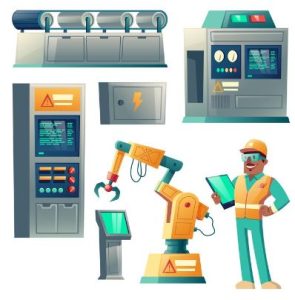
Benefits
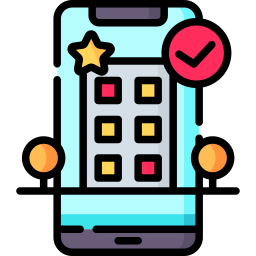
Improved resource management through data-driven insights into production processes and equipment performance.
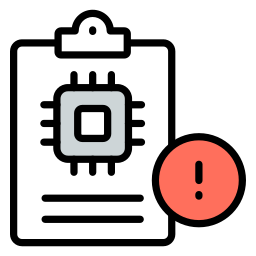
Reduced downtime and maintenance costs through proactive identification of potential equipment issues

Optimized production workflows by identifying bottlenecks and streamlining material flow.
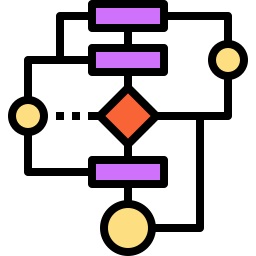
Data-driven decision making for resource allocation, production planning, and scheduling adjustments.
Case Study 3
Smart Inventory Management and Predictive Maintenance for Efficient Supply Chain (Logistics & Maintenance)
Challenge
Traditional metal manufacturing relies on manual inventory tracking and reactive maintenance practices. Metal companies struggle to anticipate material needs accurately, optimize inventory levels, and avoid stockouts or excessive storage costs. Additionally, they face challenges in maximizing equipment uptime due to reactive maintenance approaches.
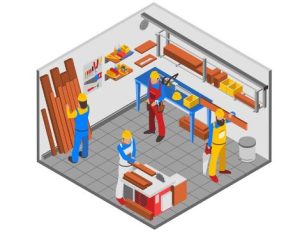
Solution
Metal companies can implement a comprehensive inventory management system with real-time monitoring capabilities. Sensors can be installed in raw material storage areas to track metal stock levels. Additionally, finished product inventories can be monitored at production facilities and distribution centers. This data can be integrated with production planning software and sales forecasts to predict material needs and optimize ordering procedures.
Furthermore, predictive maintenance practices can be implemented by equipping production equipment with sensors that monitor vibration, temperature, and other performance parameters. This data can be used to identify potential equipment failures and schedule preventive maintenance interventions before breakdowns occur.
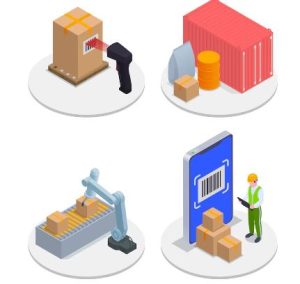
Benefits
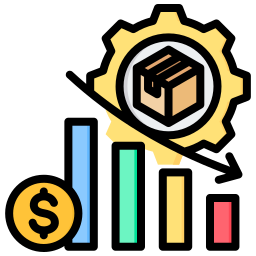
Reduced risk of production disruptions and delays by proactively managing metal inventory and anticipating material needs.
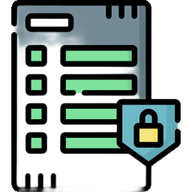
Minimized storage costs and waste by optimizing inventory levels and ordering practices.
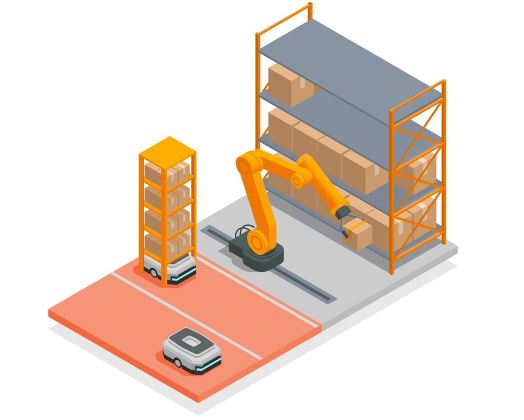
Extended equipment life and improved overall maintenance efficiency through proactive interventions.
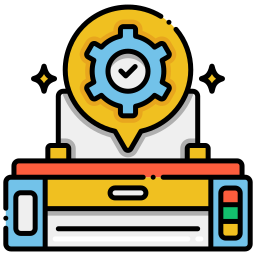
Increased production uptime and overall operational efficiency.
These cases highlight how metal manufacturing companies can leverage automation technology to address challenges across production, operations, logistics, and maintenance. By implementing robotic cutting and fabrication systems, real-time data analysis, and smart inventory management with predictive maintenance, metal companies can achieve higher production volumes, improve product quality and consistency, optimize resource utilization, and minimize disruptions throughout the manufacturing process.