Case Study 1
Smart Vending Machines with Real-Time Inventory Management and Predictive Maintenance
Challenges
Traditional vending machines rely on manual restocking and reactive maintenance, leading to stockouts, product expiry, and unnecessary service calls. Beverage companies struggle to optimize inventory levels in vending machines and ensure product availability for customers.
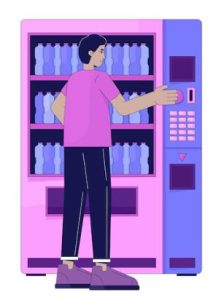
Solutions
Beverage companies can equip their vending machines with IoT sensors and connectivity modules. These sensors can track inventory levels for different beverages and transmit real-time data to a central platform. The platform can then analyze sales data and predict product demand, prompting automated restocking orders to distributors or service personnel. Additionally, sensors can monitor machine performance and identify potential maintenance issues before breakdowns occur.
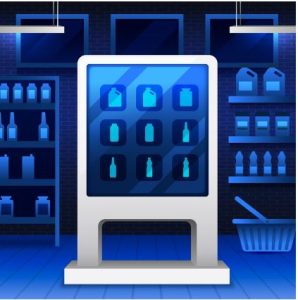
Benefits
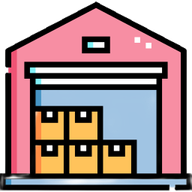
Reduced stockouts and improved product availability for customers, leading to increased sales

Minimized expired beverages and product waste by optimizing inventory based on real-time data

Streamlined restocking processes and reduced operational costs associated with unnecessary service calls.
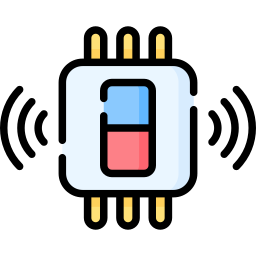
Proactive maintenance based on sensor data, preventing machine downtime and ensuring reliable operation.
Case Study 2
Connected Kegerators with Remote Monitoring and Beverage Management
Challenge
Traditional kegerators lack real-time monitoring capabilities, making it difficult for beverage companies to track keg inventory and ensure proper draft system performance. Companies struggle to optimize keg deliveries and identify potential issues before they impact customers.
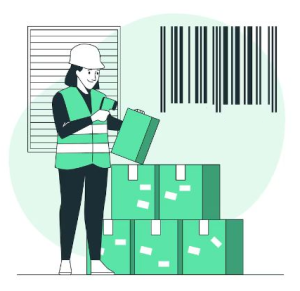
Solution
Beverage companies can offer connected kegerators to bars and restaurants. These kegerators can be equipped with sensors that monitor keg pressure, temperature, and even remaining beer volume. The collected data is transmitted wirelessly to a cloud platform accessible by the beverage company and the customer. This allows for remote monitoring of keg levels, ensuring timely deliveries before kegs run empty. Additionally, the data can be used to identify potential problems with the draft system, such as pressure fluctuations or temperature issues, allowing for proactive maintenance.
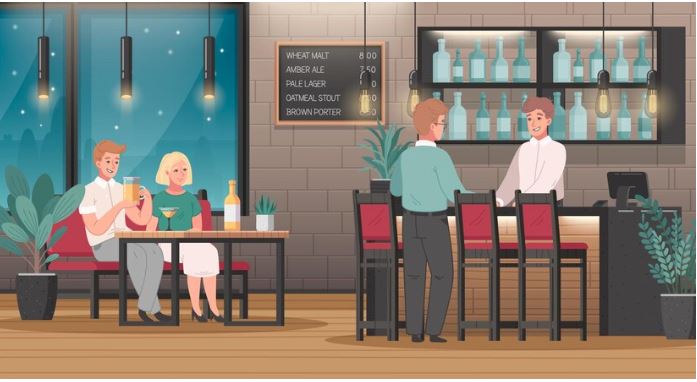
Benefits
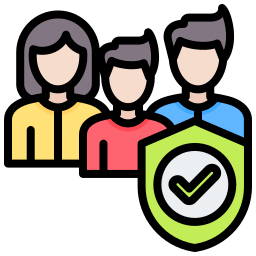
Improved customer satisfaction by ensuring consistent beverage quality and preventing interruptions due to empty kegs.
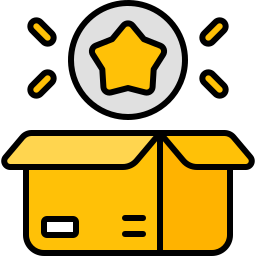
Optimized delivery schedules based on real-time keg level data, minimizing unnecessary deliveries and reducing logistics costs.
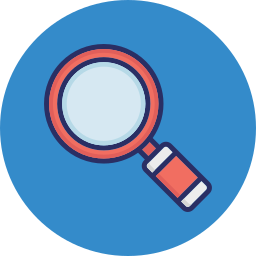
Early detection and diagnosis of potential draft system issues through remote monitoring, minimizing downtime and product spoilage.
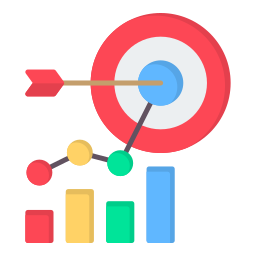
Valuable data insights into customer consumption patterns and keg rotation, informing product placement and marketing strategies.
Case Study 3
Smart Beverage Bottles with Track and Trace for Anti-Counterfeiting and Brand Protection
Challenge
Counterfeiting is a significant problem for beverage companies, leading to brand reputation damage and potential health risks for consumers. Traditional tracking methods lack transparency and may not be effective in preventing counterfeits.
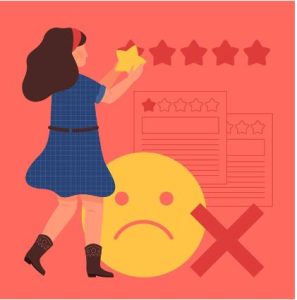
Solution
Beverage companies can explore the use of smart beverage bottles with embedded RFID tags or unique QR codes. These tags can be scanned by consumers or distributors at various stages of the supply chain. The scanned data is transmitted to a secure cloud platform that tracks the location and movement of each bottle. This allows for real-time verification of product authenticity and identification of potential counterfeit products.
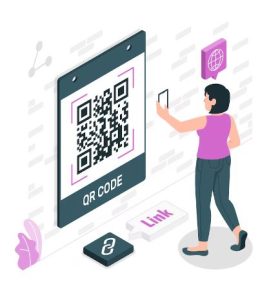
Benefits
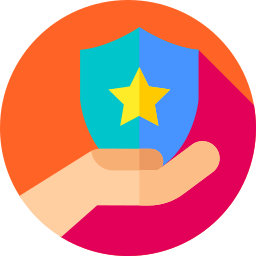
Enhanced brand protection and consumer safety by deterring counterfeiting and ensuring product authenticity.
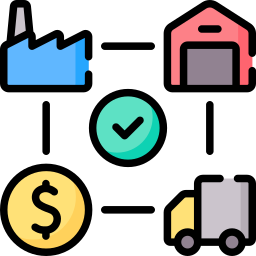
Improved supply chain transparency by tracking the movement of beverages from production to retail locations.
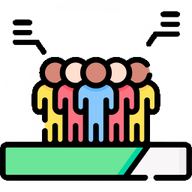
Potential for consumer engagement through interactive packaging with scannable codes for product information or loyalty programs.
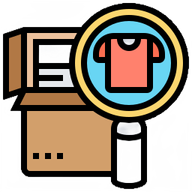
Valuable data insights into product distribution patterns and potential diversion of genuine products.
These cases showcase how beverage companies can leverage IoT technology to address various challenges throughout their operations, from vending machine management and kegerator performance monitoring to anti-counterfeiting measures. By implementing IoT solutions, beverage companies can improve customer satisfaction, optimize logistics and distribution, protect their brands, and gain valuable data insights to inform future strategies.