Case Study 1
Real-Time Tracking and Improved Visibility for Cargo Management
Challenges
Traditional cargo tracking methods often rely on manual updates and outdated information. Cargo companies struggle to provide real-time location data and ensure transparency throughout the supply chain.
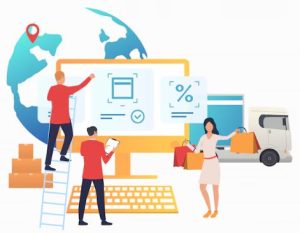
Impact
Lack of visibility into cargo location can lead to delays, missed deliveries, and difficulty managing customer expectations. Additionally, it hinders proactive intervention in case of potential problems during transit.
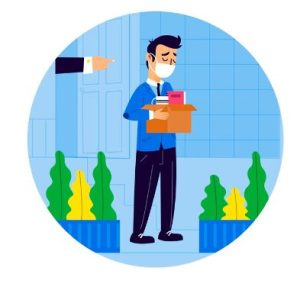
Solution
A cargo company can implement an IoT-based tracking system. This system utilizes GPS devices or RFID tags attached to containers or individual packages. Real-time data on location, temperature, humidity, and even potential tampering attempts is transmitted wirelessly and accessible through a centralized platform.
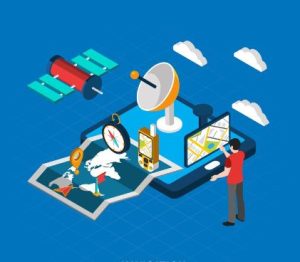
Benefits

Improved visibility of cargo location throughout the entire supply chain journey.
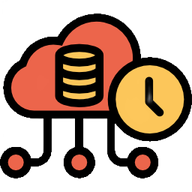
Real-time data allows for proactive management and route optimization for faster deliveries.
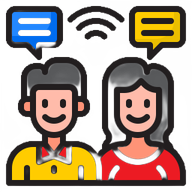
Enhanced customer satisfaction through transparent communication on shipment status.

Reduced risk of cargo theft or loss due to tamper alerts and real-time tracking.
Case Study 2
Predictive Maintenance for Optimized Fleet Management and Reduced Downtime
Challenge
Traditional fleet maintenance schedules are often reactive, leading to unexpected breakdowns and costly repairs. Cargo companies struggle to predict component failures within vehicles and optimize maintenance scheduling.
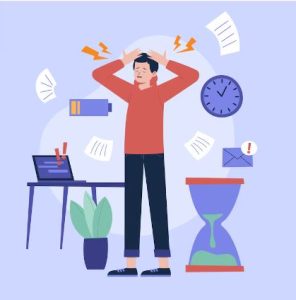
Impact
Unexpected vehicle breakdowns can cause delays in deliveries, disrupt operations, and incur significant repair costs. Reactive maintenance approaches are less efficient than preventive measures.
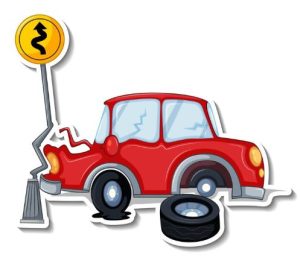
Solution
A cargo company can equip their vehicles with IoT sensors that monitor engine performance, tire pressure, and other critical components. The collected data is sent to the cloud and analyzed by machine learning algorithms. These algorithms can predict potential failures and alert maintenance crews before breakdowns occur, allowing for preventive action.
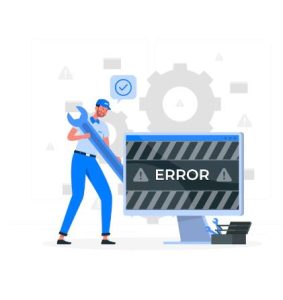
Benefits
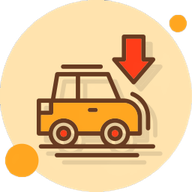
Reduced vehicle downtime through proactive maintenance based on real-time data.
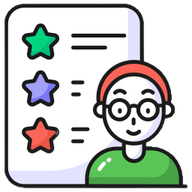
Reduced hospital readmission rates by identifying patients who may need additional support after discharge.
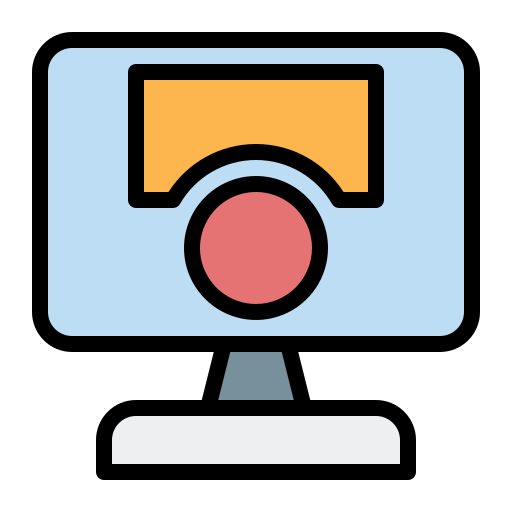
Improved operational efficiency by optimizing maintenance schedules and resource allocation.
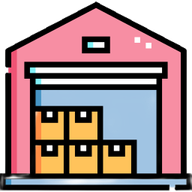
Enhanced safety by identifying and repairing potential problems before they cause accidents.
Case Study 3
Smart Warehouses for Efficient Cargo Handling and Inventory Management
Challenge
Traditional warehouse management relies on manual processes and paper-based tracking systems, leading to inefficiencies and potential errors. Cargo companies struggle to optimize storage space utilization and ensure accurate inventory control.
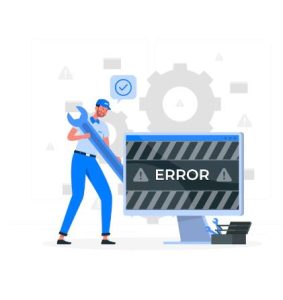
Solution
A cargo company can implement an IoT-based warehouse management system. This system utilizes automated guided vehicles (AGVs) equipped with sensors to navigate the warehouse and move cargo. Smart shelves with weight sensors track inventory levels and trigger alerts when restocking is needed. All data is integrated into a central platform for real-time visibility and control.
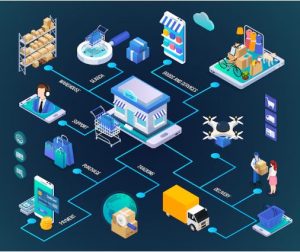
Benefits
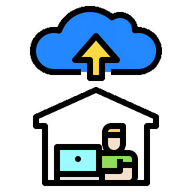
Increased efficiency in cargo handling and movement within the warehouse through automation.
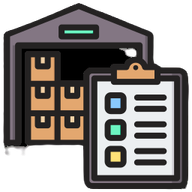
Optimized storage space utilization with real-time data on inventory levels and item location.
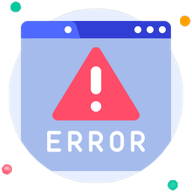
Reduced errors in inventory management and order fulfillment due to automated tracking systems.
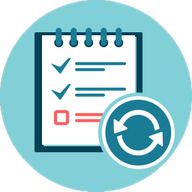
Improved labor productivity by freeing up employees from repetitive tasks for higher-value activities.